WSI ASTM D8073-16 Water Separation Instrument
WSI Water Separation Instrument – ASTM D8073-16 – WSI ASTM D8073
The CGSB have confirmed the inclusion of ASTM D8073 (IP624) in Table 1 (mandatory) of the Canadian Jet fuel specification, CGSB 3.23-2019
WSI for short is a revolutionary new technology that provides a repeatable and reliable water separation test. The WSI was developed to increase the reliability of the water separation from fuel measurement. The filter is based on 5th Edition API certified materials.
WSI ASTM D8073 Brochure: WSI Brochure
ASTM D8073-16 Listing: https://www.astm.org/Standards/D8073.htm
The WSI Owner’s Manual Is here: WSI User Manual
The ASTM D8073 Test Method, the WSI has now been added to D1655, Appendix X1.13.2, and X1.13.2.2.
The ASTM D8073 Test Method, the WSI has also been added to the CGSB, under CAN / CGSB – 3.23 – 2019.
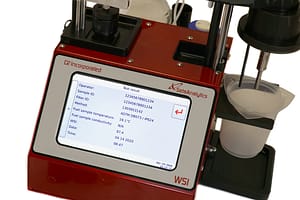
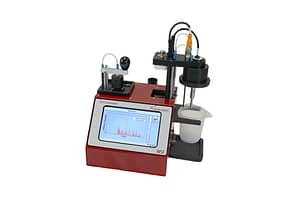
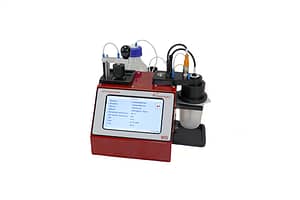
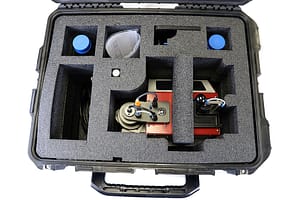

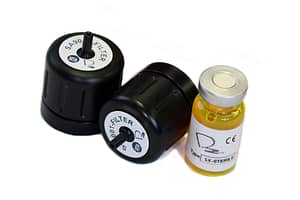
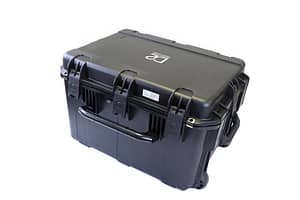
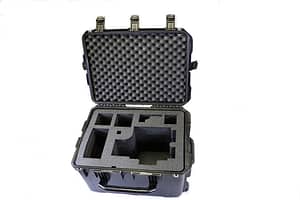
Water Separation Instrument Determining Filterability of Jet Fuel
The Water Separation Instrument WSI is a fully automated, digital, revolutionary new device that provides a repeatable and reliable water separation test.
The WSI ASTM D8073 device has several advantages over previous water separation characteristic instrument. Starting with its modern user interface, fully automated test, which is easy to use, ergonomic design that requires little user training. Human variability is eliminated from test results by the automation of the method, key examples are sample fuel water emulsion mixture by the use of a patented sonic mixer.
Automation to Improve Accuracy
The sonic mixer emulsifies the water droplets in the mixture to a uniform size, every test. The disposable filter use of API certified 5 edition materials allows for direct correlation to filter stand performance, the ultimate goal of any small scale water separation test. The WSI disposables are simpler and lower cost per test than the existing method, before additional labor saving cost are considered, resulting significantly lower cost/test. Standard Reference materials are available from D-2 allowing in-house validation as with all D-2 Products, allowing our customers to directly meet ISO Quality System validation needs, and, significantly reducing equipment return/recalibration expense.
Test Methods:
ASTM D8073-16
ASTM D1655, Appendix X1.13.2, Appendix X1.13.2.2.
CAN/CGSB-3.23-2019
FEATURES:
- ASTM Number D8073-16
- Automated measurement technology, no human error, less user training.
- Far more accurate test of water separation characteristics of jet fuel.
- Rapid screening, takes 10 minutes to run, no operator oversight needed.
- Single result, readings no impacted by weak surfactants such as SDA.
- Replicates true surfactant impact on fuel filterability, more precise, no false negatives.
- Sonic Mixer automates sample mixing: produces far better emulsification
- Labor saving – far easier to use, quicker to run, no false negatives / positives
- USB data Output connectivity, 100% Data Storage in PC FAT compatible Files
- Unit monitors consumable and waste levels reduce operator oversight.
- Field verification standards, field calibration possible.
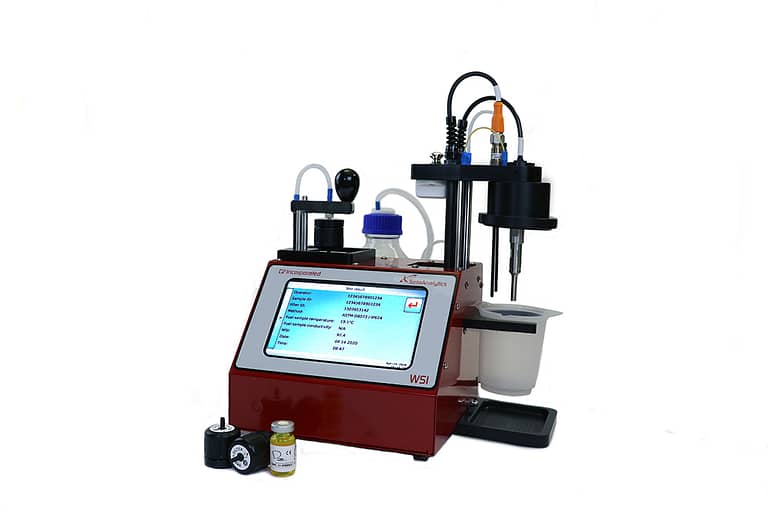
Patented Ultra Sonic Mixing
Pictured is the Ultra Sonic Mixer, a patented part of the WSI device. This Mixer automatically mixes the sample for the end user. By using an ultra sonic mixer we are able to achieve a far better emulsification of the fuel / water droplets. Also by using a known amount of power to mix the sample we get uniform water droplet size, which is key when checking filter-ability of fuel.
No More Human Error
The mixer completely eliminates the human element of sample preparation saving time and greatly increasing the accuracy of the test.
Reduces Operating Costs significantly
The WSI is designed to give rapid automatic water separation results, not only by providing a far more accurate and reliable test, but also by eliminating most of the cost associated with running this test.
Our device only requires only a low cost new disposable filter between every use. This reduces the cost to run each test dramatically as there is no more need to buy expensive test kits for every fuel sample, just very inexpensive paper filters.
Eliminates Time on Task
The operator’s will be freed up to run other tests. The WSI is fully automated, so the operator just places the sample in and let the unit run. After only 9 minutes (far quicker than the old test method) the reading will display on the digital touch screen display. In the meantime the operator can go and work on something else. Saving them labor time which is money.
Also by increasing the accuracy and eliminating the false negatives you are saving from any false incidents which can be very costly.
How to Rebuild the WSI Test Pads
If you want to rebuild your own WSI test Pads to save money on operation costs, you can! We will show you how! The above video is regarding our Sustainable Filter Holder which makes the process quite simple. You can also read our full article and see the D-2 Inc. version of this instruction video on the web post here!
WSI Test Pads Rebuilding Instructions